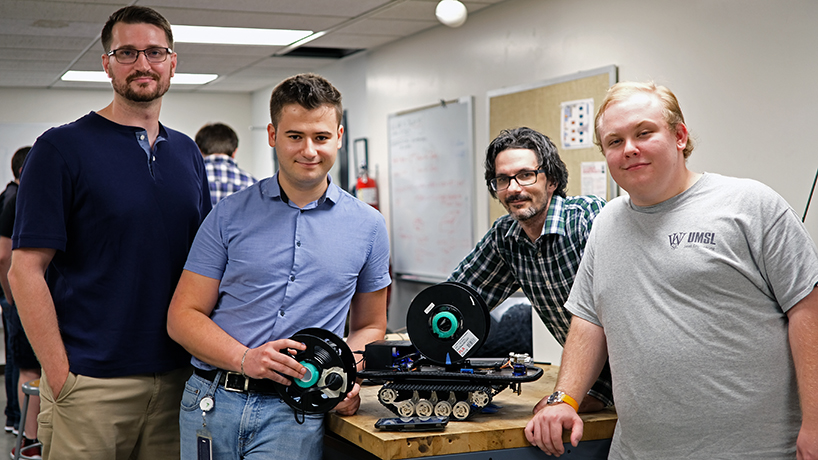
Mechanical engineering seniors (from left) Jonathan Olson, Kristian Stavri, Colin Brady and Corey Milcic built a robot that lays extension cord during their capstone course. (Photos by Jessica Rogen)
Have you ever found drying yourself with a towel to be too much effort?
Well, here’s the product for you: The Body Dryer, a full-physique experience that takes the user from soaked to dry in under one minute thanks to the power of two HVAC air blowers.
The only problem? It’s not quite to market yet.
A group of three mechanical engineering students – Laura Bailey, Luke Maichel and Nickalous Zuelke – made the prototype for their capstone course in the University of Missouri–St. Louis/Washington University in St. Louis Joint Undergraduate Engineering Program. Their group was one of 14 small teams challenged to build a working prototype with only $200 and eight weeks to get the job done.
Mark Jakiela, mechanical engineering program director and course instructor, generated briefs for this summer’s cohort of students but welcomed companies or organizations interested in designing the problems as the Donald Danforth Plant Science Center did in 2017. New this year was the addition of Craig Giesmann, an engineer from Ameren, as an adjunct co-instructor. Many of the faculty in the program work full time in local industry, and teach in the program in the evenings.
Among the projects were a portable car lift, emergency flood walls, an electric powdered-drink stirrer, a way to reduce soil compaction for agriculture and more.
“It’s where we all prove everything out,” Jakiela said. “The projects are supposed to have considerations of everything they’ve studied so far applied to a real-world problem. The students have to generate ideas, do what’s called an embodiment, where they have to figure out how they are going to build it, and then go ahead and do it.”
Students have to take considerations such as size and the thickness of the materials into account. Patrick Koch, Franchesca Petersen and Jennifer Sommerfeld discovered that while working on a hand-powered spirograph – a drawing robot – intended for a playground.
“It had to be small enough to be made of disassemblable materials,” Koch said. “It’s a kids’ toy, so the rotating gears had to be enclosed because there was a safety concern. It also had to be up to codes and standards for building.”
Simpler designs often worked better, something the Body Dryer team discovered while attempting to achieve even air flow throughout their dryer’s arch. The group tried designing complicated external nozzles but ended up going with a simplified internal option.
They found other rewards came from simplicity. Comprised entirely of common materials that could be found at a hardware store, their prototype is easy to install and maintain and uses less energy than washing and drying towels.
Joe Biermann, Brittany Gray and Nathan Hopper designed a magnetic stirrer for powdered drinks and smoothies. They based it around a computer fan in a 3-D printed base.
Another challenge of the course was learning how to work in teams. That’s something Colin Brady discovered while working on his project with Corey Milcic, Jonathan Olson and Kristian Stavri.
“It’s essential to trust your team,” Brady said. “Eight weeks is a short time. I trusted my team the whole way through, and we respected each other to just go and do it.”
Trust with that time crunch was critical for the group. They built an articulated cord delivery robot, which puts down one 25-foot extension cord, attaches a second and lays it down then returns to the start to resupply. The group designed the rugged, small-scale robot with an ultrasonic sense for object detection with space exploration in mind.
But trust turned out to be just one part of good teamwork. Maintaining good communication was another, noted Bobby Westeen, who, along with Tyler Micke, worked on creating an adult car seat intended to increase safety.
“The biggest thing was the ability to solve problems,” Westeen said. “That and learning new things quickly.”
The two ran through various solutions in the first weeks of the course before settling on a buckle-in seat with a four-point, quick-release harness similar to what’s used in race cars.
“It’s simple and silly,” he said. “But it works.”