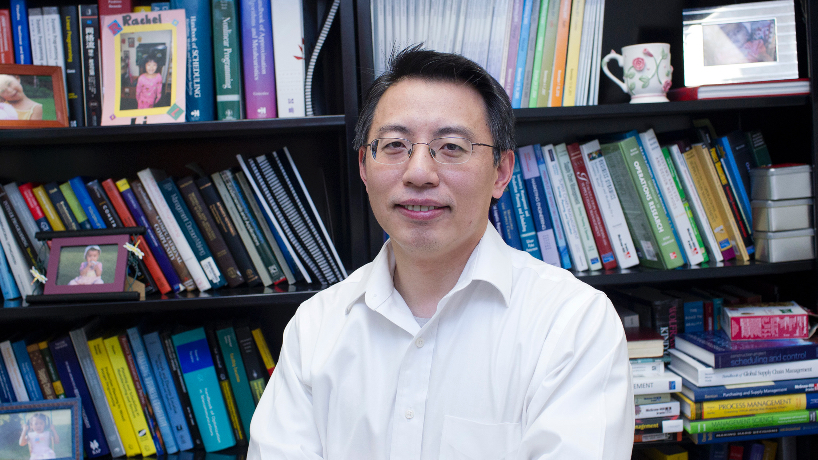
The coronavirus has companies restructuring their supply chains based on data-driven analytics. For researchers like Haitao Li, it presents an opportunity to help firms take a proactive approach to planning for crises. (Photo by August Jennewein)
With shortened hours, shoppers spaced six feet apart and a limited number of customers allowed at once, trips to the store have become radically different in the past month as companies work to slow the spread of the novel coronavirus.
The effects of COVID-19 are also apparent on shelves, where familiar brands may be missing from their usual spots. According to Haitao Li, professor of supply chain and analytics at the University of Missouri–St. Louis College of Business Administration, it’s the result of disruptions in the global supply chain.
“An immediate cause is supplier disruption,” he said. “Starting with China, companies and manufacturers shut down their operations for weeks, so that’s going to impact the global supply chain of U.S. manufacturers.”
The impact will especially affect the electronics industry, as components and parts come primarily from countries hardest hit by COVID-19. The pharmaceutical supply chain may also experience a shortage of raw chemicals usually supplied by companies in China and India.
Ultimately, the coronavirus will impact virtually every industry in some way, although there may be some lag. Fortunately, businesses can adjust their supply chains to lessen the impact of disruptions.
In usual circumstances, companies utilize a global supply chain model primarily to reduce costs and grow their consumer base. They also benefit from the expertise and skills of employees working for overseas suppliers.
Many companies using a global model keep their inventory as lean as possible to maintain operations while reducing cost. With a disruption as significant as the pandemic, being lean creates risk. Companies may not have anticipated a shortage of supply or a sharp increase in demand for their products.
The most noticeable example of increased demand is toilet paper.
“There is a good explanation from the supply chain perspective,” Li said. “Toilet paper, especially with bulk sizes from Costco, generally lasts for about two or three months. Its supply chain typically expects a longer lead time, but now the demand is increased so much all of a sudden. That’s why we see the immediate shortage of toilet paper.”
When facing a supply chain disruption, companies can respond in two ways – reactively and proactively.
A reactive approach is necessary when a crisis is already in motion and involves adjusting inventory and sourcing to fit the market.
“Companies should think about reconfiguring their supply chain in terms of sourcing decisions,” Li said. “Where should they source? What alternative suppliers should they use now to mitigate the loss? Companies should be more agile and alert, more flexible in their inventory and stock decisions to make sure they have enough supply to support their production needs and the right amount of inventory to satisfy market demand.”
A proactive approach involves planning for a supply chain disruption before it occurs, using analytical methods and data to guide the decision-making process.
“Companies can actually design a system that is efficient and robust so that their practice is more prepared for a disruption like this,” Li said. “For example, if a company can factor in the huge cost of supply disruption, we can come up with multiple suppliers instead of just one. Using one supplier is typically less costly, but it’s more vulnerable to supply disruption. We may suggest that a company utilize multiple suppliers, not just those in China and India but some located locally. They’re more expensive, but that will certainly help mitigate the negative impact of such supply disruptions.”
The global supply chain has faced disruptions before, such as the 2011 Japan tsunami, but the magnitude of the pandemic’s impact is unprecedented. As a result, most companies are responding reactively to changes in the market.
For researchers, this presents an opportunity for innovation.
“I want to emphasize the importance of supply chain management and leveraging analytics to help our society and our businesses come up with informed and data-driven decision-making to cope with such a crisis,” Li said. “This is the right time for companies to be more careful than before to optimize their operations.”
Although an abundance of data helps executives make informed decisions, Li believes the key to a successful supply chain is being flexible and able to quickly adapt to changing markets. Models that have worked for decades will likely need to be revised.
Supply Chain and Analytics Department faculty members are utilizing their expertise to help mitigate the pandemic’s effects. Trilce Encarnacion and Shakiba Enayati, who will join UMSL in the fall semester, specialize in humanitarian logistics and resource allocation in the medical supply chain. Li and Professor James Campbell are conducting research on using drones to deliver vaccines in less developed regions, as well as researching risk assessment and mitigation in the pharmaceutical benefit management industry.
The Supply Chain Risk and Resilience Research Institute is poised to help guide companies through revising their supply chains to better respond to crises. The department is also working with its advisory board to host a brainstorming session and an online panel discussion on how COVID-19 is affecting Missouri companies.
“We are all ready to contribute our research to the practice of coping with crises such as this,” Li said. “We’re expanding our view in thinking about crises similar to this, not just this one event. This is a critical moment, but at the same time, for researchers it also creates an arena of opportunities for us to be creative, especially here at UMSL.”